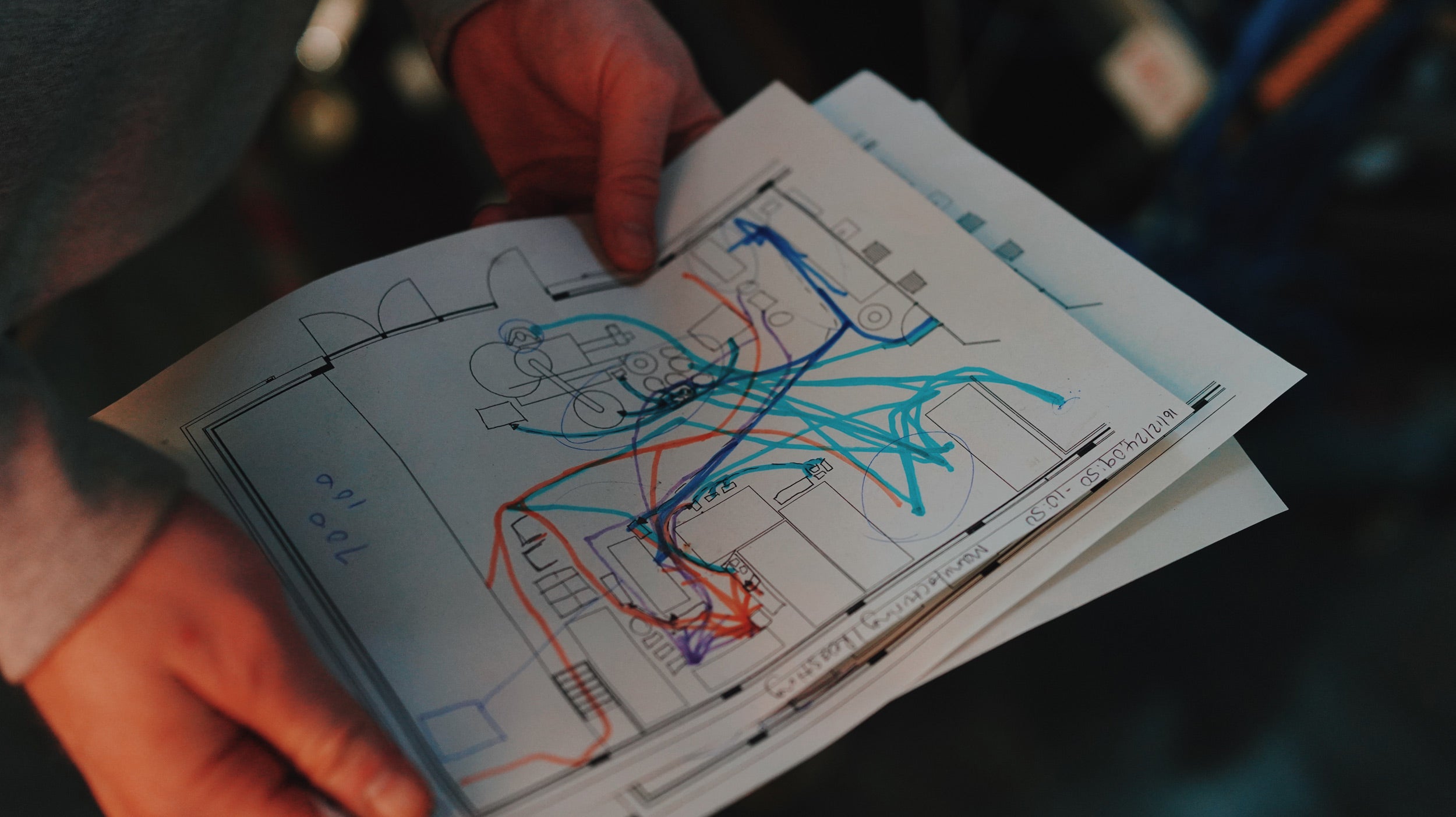
A Fresh Start for the New Year: Moving Our Production Space for Efficiency and Growth
When costs all around us are rising—whether it’s commodity prices, global logistics, NI contributions, Business Rate Support, or the Real Living Wage—we’re determined not to pass unnecessary waste onto our customers. By focusing on the costs we can control, we’re making sure our customers get the best value without paying for inefficiencies.
This mindset has inspired us to take a fresh look at how we run things. As we step into the new year, we’re not just setting new goals—we’re also rethinking how we change behind the scenes. After taking a closer look at our production area, it became clear the current layout wasn’t helping us grow the way we want. One of our key principles is to stay lean—creating more value while wasting less. So, we decided it was time for a change. In this blog, we’ll take you through our journey of reorganising and moving our production space, the steps we took to make it happen and how it’s already making a difference in how we work and serve our customers.

Our Philosophy: Lean and Efficient
At the heart of our business is the commitment to being lean. This approach encourages us to focus on value creation and operational efficiency while minimising waste. Lean isn’t just a buzzword—it’s changing our mindset that influences every part of our operations. We focus on eliminating the 8 deadly wastes in our work environments, which include:
1 - Overproduction is the first waste, having too much stuff.
2 - Excess inventory, having too much stuff means things can go to waste.
3 - There are then defects (think Gherkins in Mcdonalds).
4 - Over processing, we have to handle and re handle our processes.
5 - Transportation we have to move and remove all this extra stuff.
6 - Excess motion during manufacturing orders.
7 - Wasted time, delays in the flow of value to customers.
8 - Wasted Employee Potential, we don't wont to be stuck in the mud we want to be innovating ways by which we can make Coaltown better looking for world class products, performance and customer experience.

Why We Moved Our Production Area
After a thorough evaluation of our current layout, it became clear that the existing setup was causing unnecessary motion, poor utilisation of talent, excessive transportation and even extra processing. The flow of work was hindered and the time spent moving between workstations was leading to inefficiencies.
How We Decided on the New Layout
To make informed decisions, we started with some simple yet effective research. Katrina, one of our team members, mapped out everyone’s footpaths during a busy afternoon at our HQ Roastery. What stood out immediately was the amount of wasted motion. Gary, our head roaster, covered the entire floor, moving between various areas to roast our house coffees. Adrianna, who is responsible for manufacturing, found herself making constant trips to the printer. On the other hand, Buddug, had a more controlled and streamlined space. This visual representation helped solidify our thinking that a change was necessary for a smoother and more effective workflow.

Timing the Move
To avoid disrupting daily tasks and maintain operational flow, we strategically planned the move for the first Friday after our Christmas closure. We ensured all wholesale and retail orders were dispatched before the change to minimise the risk of unnecessary stock being moved around or potentially damaged during the process. We created a detailed checklist and timeline, so each team member knew their role, from cleaning and organising to using the forklift for heavy lifting. This way, we were able to execute the move with minimal disruption and maximum efficiency. Importantly, we made sure to keep the disruption to a minimum for office staff, allowing the production team to take the lead in executing the transition.
Utilising Talent
The success of our move relied heavily on the strengths and skills of our team. By assigning clear roles and responsibilities for each task, we ensured that everyone’s talents were maximised. Whether it was cleaning, reorganising production zones, or operating the forklift, each team member played a crucial role in the transition process. This approach not only optimised our time and resources but also provided opportunities for staff to contribute in meaningful ways outside of their usual roles.

How Did It Go?
Reflecting on the move, the feedback from our team has been overwhelmingly positive:
"I feel it was a really productive day. The team worked really well together and everyone worked hard to achieve our goal. The space has now got a better flow, limiting wasted motion and time. It makes sense for everyone’s roles, we can now work more smoothly and hopefully, in time, we’ll see the benefit in our roasting and manufacturing times. I was really proud of my team." - Buddug

The new layout has made a difference. There’s a clear improvement in the flow of work, from roasting to dispatching. Employees no longer have to navigate back and forth across the room to perform their tasks and our entire production cycle feels more cohesive. The new setup enables the team to be more effective and efficient, ultimately improving both the quality of our products and the experience for our customers.
This move represents more than just a physical rearrangement of our production space. It’s about aligning our operations with our core values of efficiency, minimising waste, change and creating value at every turn. By taking the time to assess, plan and execute the changes, we’re confident that the benefits will be felt in our roasting, manufacturing and dispatch times. We’re excited about the possibilities that the new layout opens up and look forward to seeing the positive impact on both our team and our customers in the coming months.
As we continue to grow, we’ll keep leaning into our philosophy, making smarter, more efficient decisions that help us deliver the best products to our customers, while providing the best environment for our team to thrive. Here's to a productive and leaner year ahead!
Leave a comment
This site is protected by hCaptcha and the hCaptcha Privacy Policy and Terms of Service apply.